June 6, 2024 — “He encouraged me to do a startup; If he hadn’t encouraged me, I probably wouldn’t have done it,” says Pritesh Yeole, as he reflects on his career journey. The “he” Pritesh is referring to–Uday Vaidya, aka the Kevin Bacon of Composites–has a knack for connecting talent and inspiring entrepreneurs.
“They’re like free birds honestly,” Uday describes his latest graduate students starting their own businesses. “No matter how good a big company is, they would be constrained by protocol. Now they are free to explore and drive innovation. From a pure innovation perspective, the more you can cut down the bureaucracy and red tape, the faster innovation can move. Otherwise, you’re killing it.”
He should know because he’s worn many different hats during his career, keeping his finger on the pulse of industry and the cutting edge of innovation. He’s currently Chief Technology Officer for IACMI—The Composites Institute® and the University of Tennessee – Oak Ridge National Laboratory (UT-ORNL) Governor’s Chair in Advanced Composites Manufacturing.
Perhaps giving graduate students space and confidence to be innovators is his secret sauce. In just the past few years, Uday has motivated at least six students to take their research to the next level: commercialization.
“It really hasn’t been strategic for me,” he confesses. “I don’t try to force any students to think that way, but it’s the nature of the work that we do. They also get a lot of exposure to industry and networking through events like CAMX, SAMPE and IACMI Members Meetings. It’s a natural progression and they start thinking hey, maybe I could do this.”
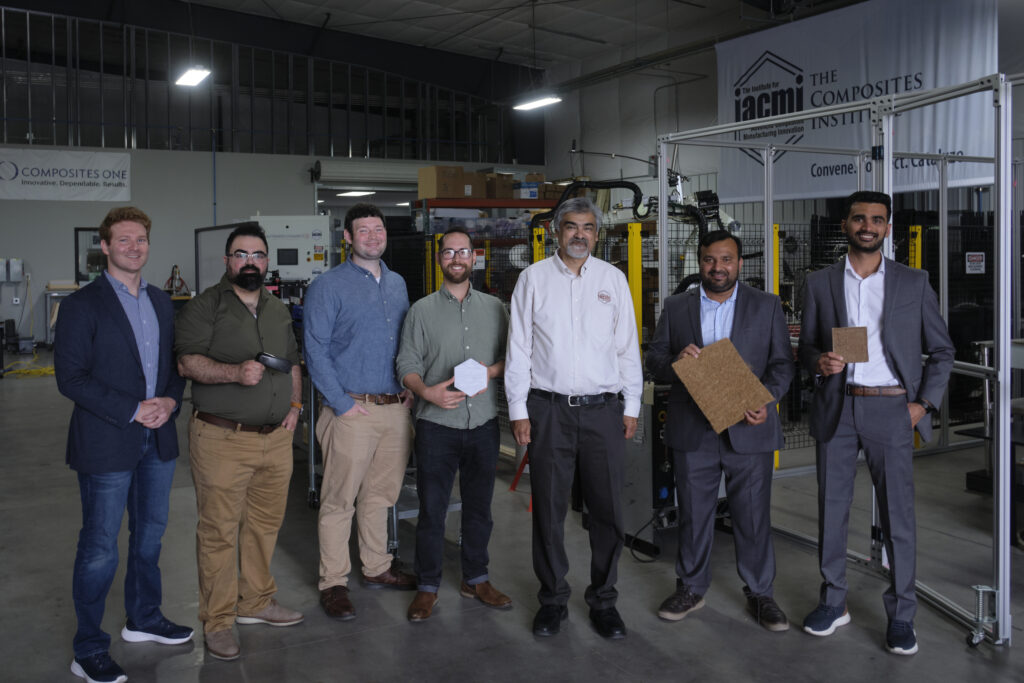
Power of the Ecosystem: Aligned Composites Technology
It’s no exaggeration to say Uday’s mentorship has been life-shaping for Pritesh: “He was the first person I met in the U.S.” After getting his master’s under Uday at the University of Alabama at Birmingham (UAB), Pritesh followed him to Knoxville to complete his PhD at UT.
Pritesh and his business partner, Vinit Chaudhary, are still in the early stages of their company, Aligned Composites Technology (ACT), but they already have 14 years of combined experience in composites. Focused on reimagining technical nonwovens for the composites industry, ACT is exploring ways to make intermediates stronger, more affordable, and sustainable. In their process, recycled carbon fiber and natural fibers like coir and hemp often start as a tangled mass. Vinit and Pritesh are precisely aligning and blending these fibers into usable mats and yarns, finding multiple applications for them, such as automotive interiors and cladding retrofit envelops in infrastructure.
They see particular opportunities in natural fiber composites. Vinit says, “To reduce the carbon footprint and make composites recyclable at the end of their life, if we can reduce or eliminate synthetic fibers such as glass fibers with natural fibers, why not do it?”
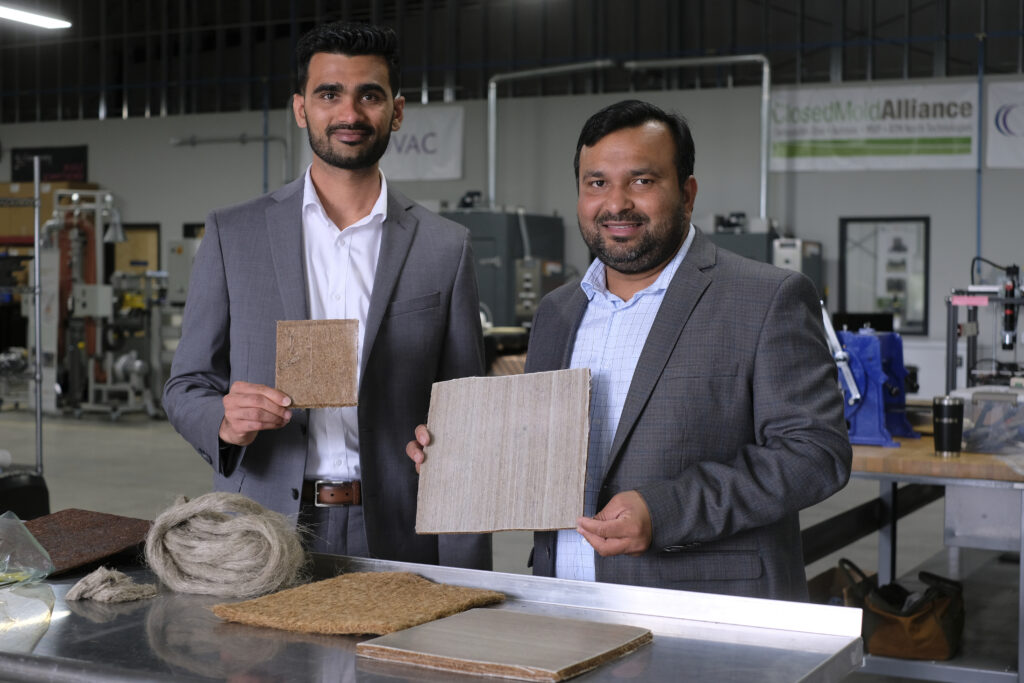
One of the biggest pieces to de-risking startups is access to a supportive ecosystem. For ACT, that’s meant being part of the Spark Cleantech Accelerator program at UT Research Park, being one of the first five recipients of the UT Chancellor’s Innovation Fund award, and Vinit being selected as a 2024 finalist for ORNL’s Innovation Crossroads. Through support from the Department of Energy, IACMI comes alongside those resources to connect startups with potential clients and supply chain vendors to further clean energy solutions. Because of the ecosystem, ACT has financial support and expert advice as they grow.
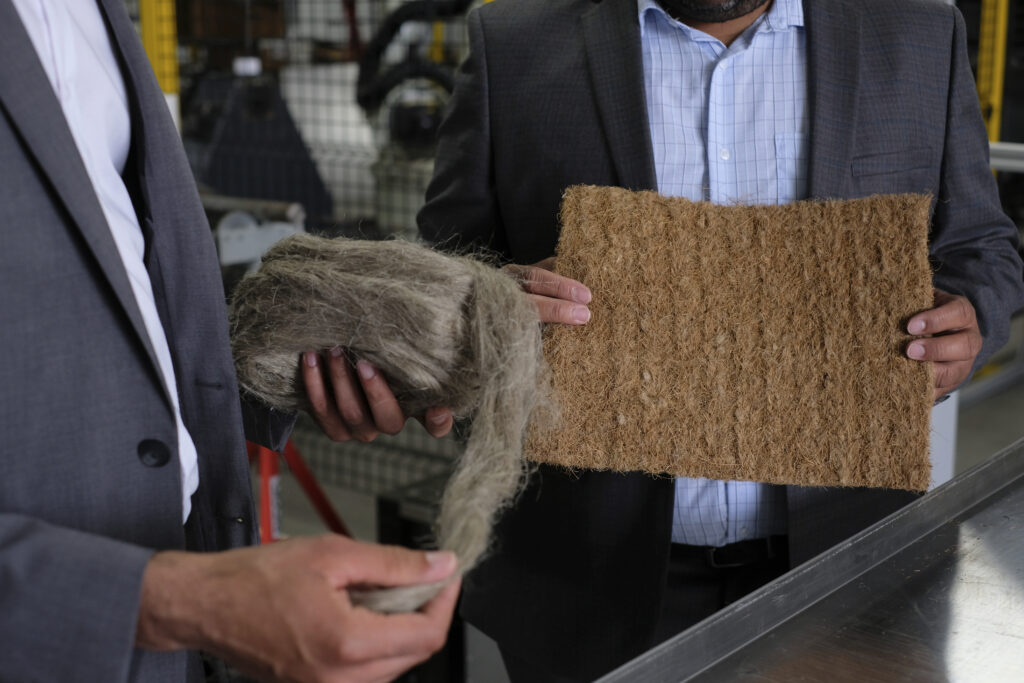
Uday adds, “There can be fear in the unknown, but I think this generation is more likely to embrace risk, to be risk takers. Part of that is they’re not completely on their own, having to raise the capital they need and figure out the specifics of starting a company. They’re not going to be out in the cold, even if it doesn’t work out.”
Ecosystem of Entrepreneurs: ThermaMatrix, Vitriform3D, Endeavor Composites
The ecosystem of support is mentioned time and again by other entrepreneurs who have emerged from under Uday’s wing: Hicham Ghossein of Endeavor Composites, Alex Stiles and Dustin Gilmer of Vitriform3D, and Ryan Spencer of ThermaMatrix to name a few. They’ve all benefited from being in cohorts of Innovation Crossroads and Uday’s mentorship at UT but are at different stages of business development.
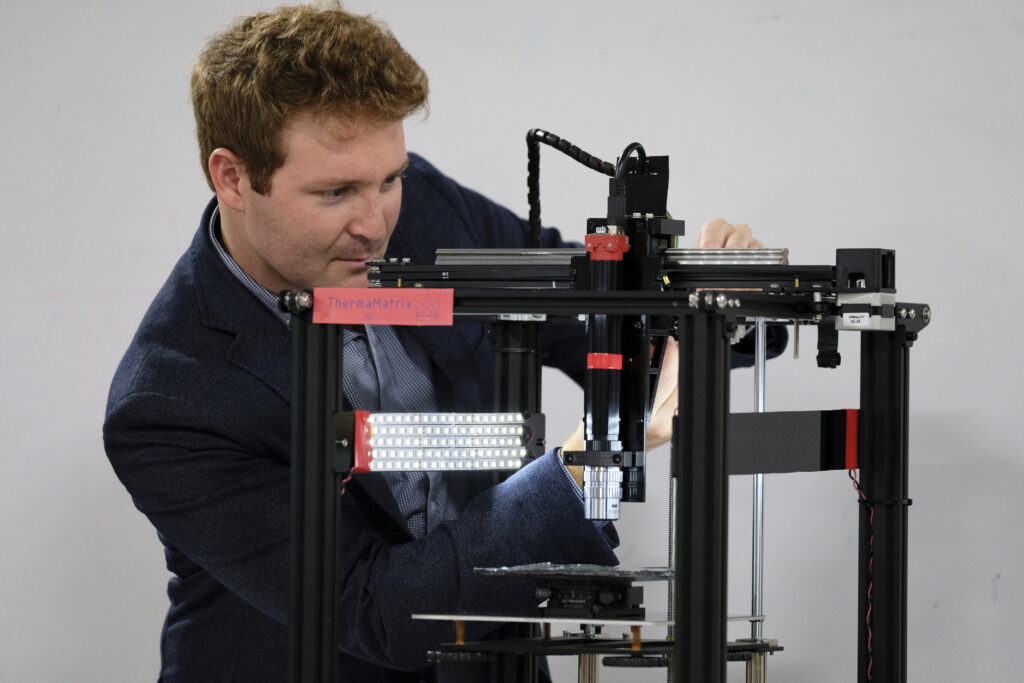
In August 2023, Ryan started ThermaMatrix to provide rapid inspection for Clean Manufacturing. He’s developed optical, non-destructive technology that’s ten times faster at a tenth of the cost of current technology: X-rays. And since most manufacturers don’t have the ability to utilize X-rays due to inspection speed and cost limitations, ThermaMatrix’s vision inspection system allows manufacturers to access these capabilities. This gives them a new way to inspect a broad range of materials and sizes—from metals to composites, from something as large as an aircraft wing to a fiber smaller than a human hair.
With a process called Digital Image Correlation, Ryan heats up a material and then monitors its thermal expansion with imaging. The novel vision inspection system uses big data and photonics to measure an array of critical defect parameters of products such as chemical storage tanks, rail tracks, and plane parts. By identifying potential issues like cracking and delamination, ThermaMatrix could enhance the safety and reliability of storage tanks for combustible fuels.
“I love bringing this level of safety to the world,” Ryan says. “When I started to do my customer discovery process, I realized how many companies could benefit by adding to their quality control and inspection capabilities. ThermaMatrix will initially support the composites industry by validating model simulations. We will then move to embed our inspection systems in-line with the manufacturing process. This opportunity started as a resume builder but has now become a calling and a dream.”
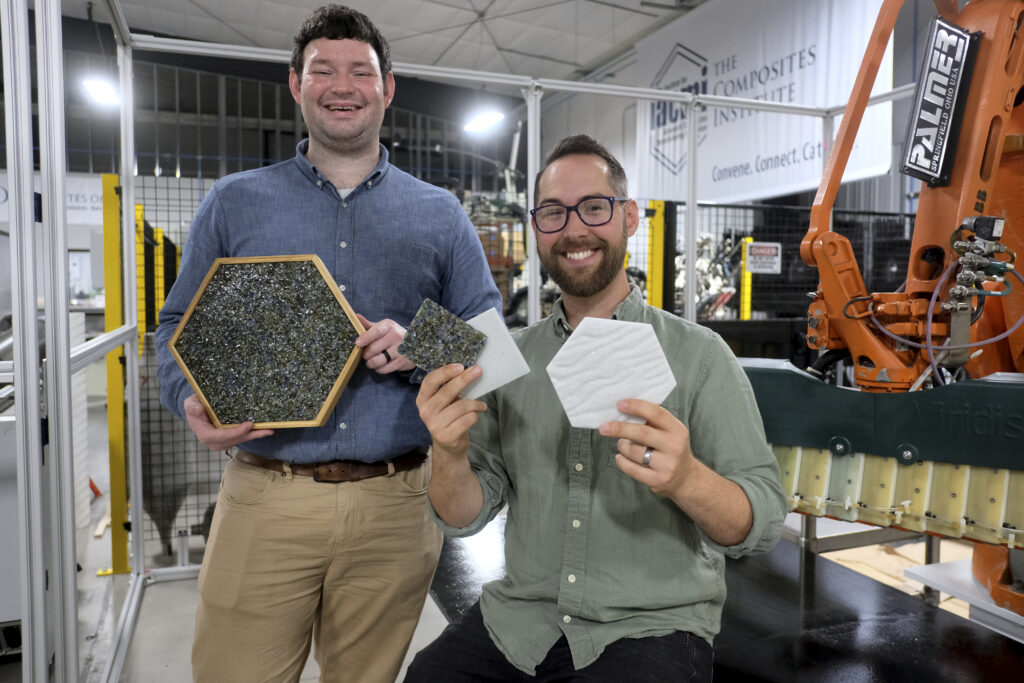
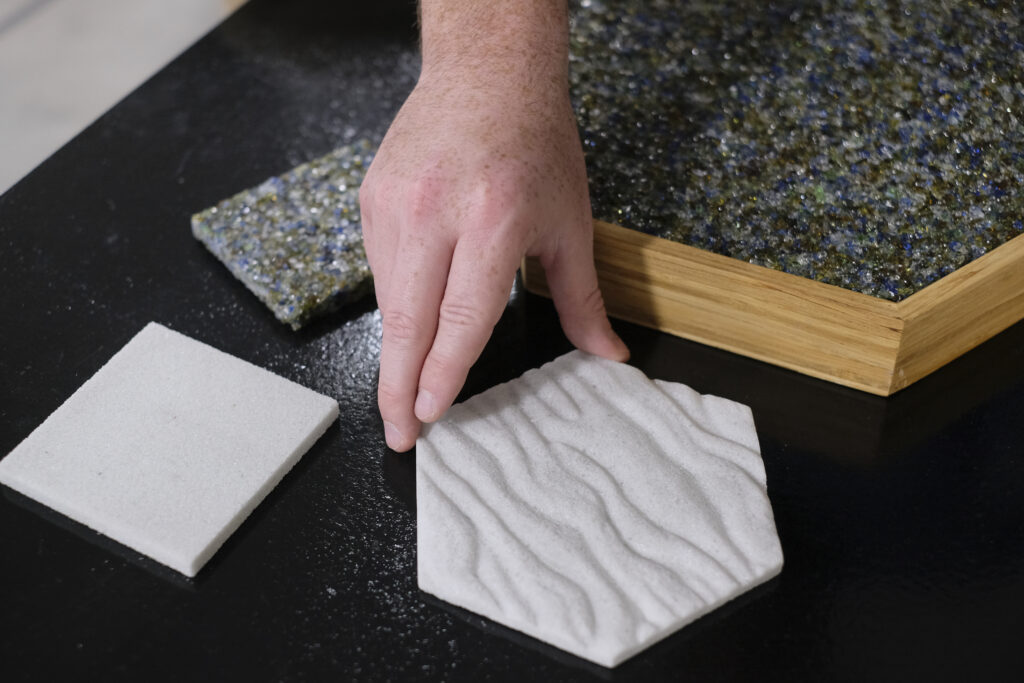
“What makes IACMI so unique is that it can help us tap into both industry and academic expertise that we can use all along our development process,” says Alex. “IACMI provides critical access to the network that we will need to commercialize our technology.”
One of IACMI’s newest members, Vitriform3D will soon be using a robotic arm that 3D prints sand at the IACMI Collaboration Facility. Alex is upgrading the equipment originally used in the foundry industry to print engineered stone with a combination of recycled glass powder and proprietary high strength binders. This additively manufactured composite material will be similar to a quartz countertop, with high hardness and good thermal stability. Alex and Dustin are exploring uses such as tooling for compression molding and autoclave as well as low embodied-carbon building products including decorative tile and wall cladding.
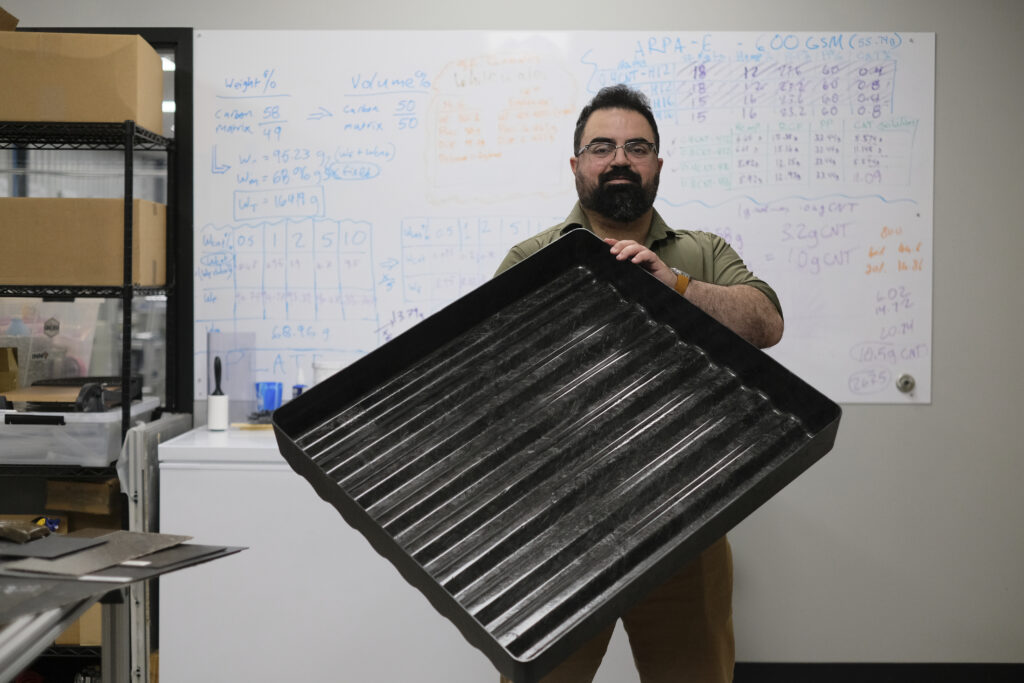
Also located at the IACMI Collaboration Facility, Endeavor Composites has been pioneering high performance, low cost, and zero-waste nonwoven reinforced composites that support a circular economy for five years. With the addition of a wet laid roll-to-roll line, they will now be scaling up their offerings to include continuous manufactured rolls of isotropic nonwoven fabrics, which should give them positive recurring cash flow by the end of 2024. In growing his customer base to 32 clients, Hicham has created five full-time and three part-time jobs. One of those jobs is another UT graduate, Matthew Saussen, who gained valuable work experience during his undergraduate years at the Fibers and Composites Manufacturing Facility led by Uday. Once again, the power of the ecosystem.
“Absolutely, IACMI has been instrumental in connecting us with suppliers, customers, and access to facilities and equipment,” Hicham says. “Being an IACMI member has been the best return on investment we ever made.” That impact can build as IACMI begins 2.0 projects. Active in multiple IACMI working groups, Hicham hopes to be part of upcoming projects that address recyclability in the transportation sector.
Even more interesting than their individual successes is how each of these companies are cross-collaborating. Between them, they’re already tackling hydrogen storage R&D, combining recycled nonwovens with 3D printing, and preparing a cladding panel from recycled glass and natural fiber composite. Vinit adds, “This will help us create insulation envelopes that are energy efficient and cost effective.”
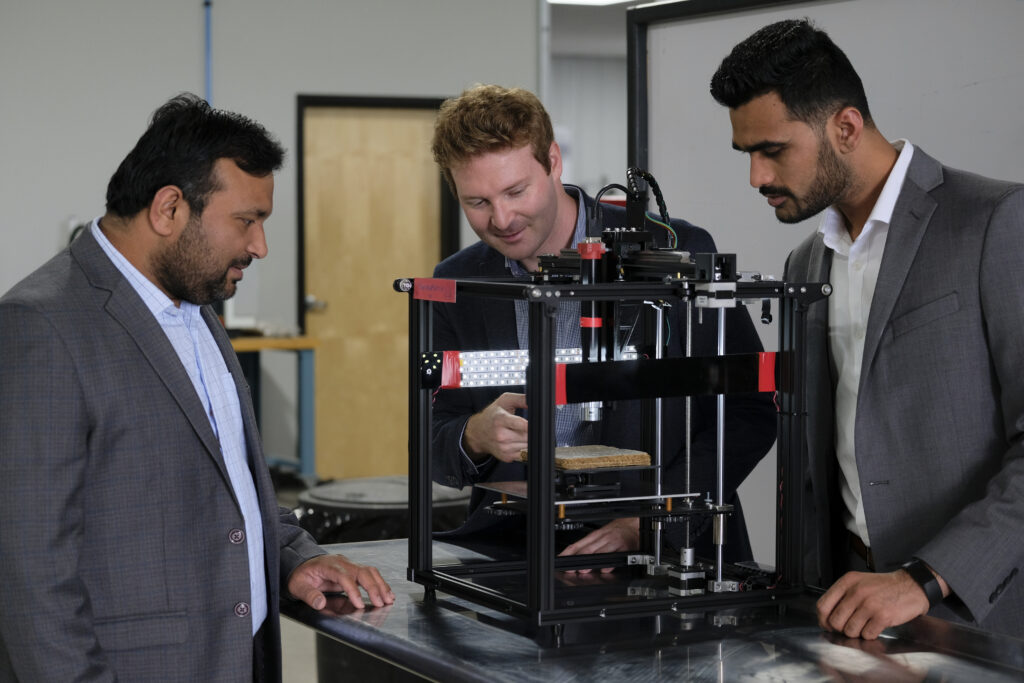
Entrepreneurship is Hard Work
These are just a few of the 10,000 students Uday has impacted over his 32 years in teaching. For these entrepreneurs, he’s gone beyond traditional support and has challenged them to be real-world problem solvers. Don’t just envision it. Make it happen. He knows they’re on a high risk, high reward path because he’s done it himself.
In 2006, Uday and two UAB colleagues won the Alabama Launchpad business competition with an aeroshell composite product they developed for the U.S. Army. That led them to founding Innovative Composite Solutions (ICS LLC). Uday’s team also developed and commercialized above-the-ground tornado resistant composite panels that can be installed in a residential closet or bathroom. While the homeowners use that space as intended, in the event of EF4 winds up to 200 miles an hour, that becomes a safe space. They also worked with military field doctors to develop abdominal tourniquets made of composites for warfighters.
Uday warns, “Entrepreneurship is hard, hard work. You start with a spark, it lights up quickly but many times, it dies away. You encounter financial issues or some glitch in the road. It’s very easy to get demotivated. It will go great at first, all accolades and claps, and then what?”
To that, Vinit responds, “I’m not afraid of failures. Coming from a family with multiple retail ventures that didn’t all work out, I’ve seen them overcome business barriers. Pritesh and I have faced several obstacles, but I’m not stressed about them. Drawing from my family’s experience in retail entrepreneurship, I’m ready for the next chapter in the hard tech industry because I know Knoxville is the perfect place to scale up our technology.”
If selected, Vinit is excited about what being part of the two-year Innovation Crossroads program could mean for him: a personal living stipend, health insurance, travel allowance, a grant for R&D at ORNL, and comprehensive mentoring assistance. For now, he and Pritesh are focused on generating their material portfolio and talking with industry to ensure they’re addressing real client needs.
Their road may not be easy, but they won’t be alone. Behind them will be a quiet, humble mentor cheering them on with this important advice: “The value of innovation to benefit society is simply amazing, but determination to succeed is of paramount importance. Keeping that level of optimism is going to be very key. Everything else will fall into place eventually. You have to believe in your cause.”