April 4, 2023 – Infinitely recyclable materials…when you think about the significance of using them from a sustainability and economic perspective…the possibilities are exhilarating! It’s like when you discovered as a kid that you could light a candle, drip some wax, let it cool and then melt it again and again. Or the first time you ran a 3D printer, turning plastic filament into whatever shape you could imagine. Now picture using 3D printing technology with glass—one of those infinitely recyclable materials that all too often is destined for landfill—and you’ve got a brilliant business model. You’ve got Vitriform3D.

A Start-up is Born
Pulled from the Latin word vitri for glass, Vitriform3D is forming new products through 3D printing. With their patent-pending technology, they plan to make coasters, tiles, countertops, even architectural accent walls by embedding recycled glass into 3D printing. It’s a small start-up for now of only Alex Stiles and Dustin Gilmer, who may have never met without IACMI – The Composites Institute. We joke, “All roads lead to Uday Vaidya,” and in this case, it’s true. Dr. Vaidya, Chief Technology Officer for IACMI, was Alex’s advisor during his PhD program at the University of Tennessee, Knoxville (UT). In one of Uday’s many collaborations with outside research groups, Dustin and Alex first worked together on novel methods for 3D printing washout mandrels for composites.
This initial collaboration led Dustin and Alex to brainstorming as entrepreneurs. Alex had been frustrated by the lack of glass recycling options in Knoxville and thought composites manufacturing could be the answer. Dustin had devoted years to developing expertise in binder jetting, an incredibly flexible 3D printing method. Binder jetting uses virtually any powder material feedstock–from ceramics to polymers to metal—so why not glass? And with this idea, Vitriform3D was born!
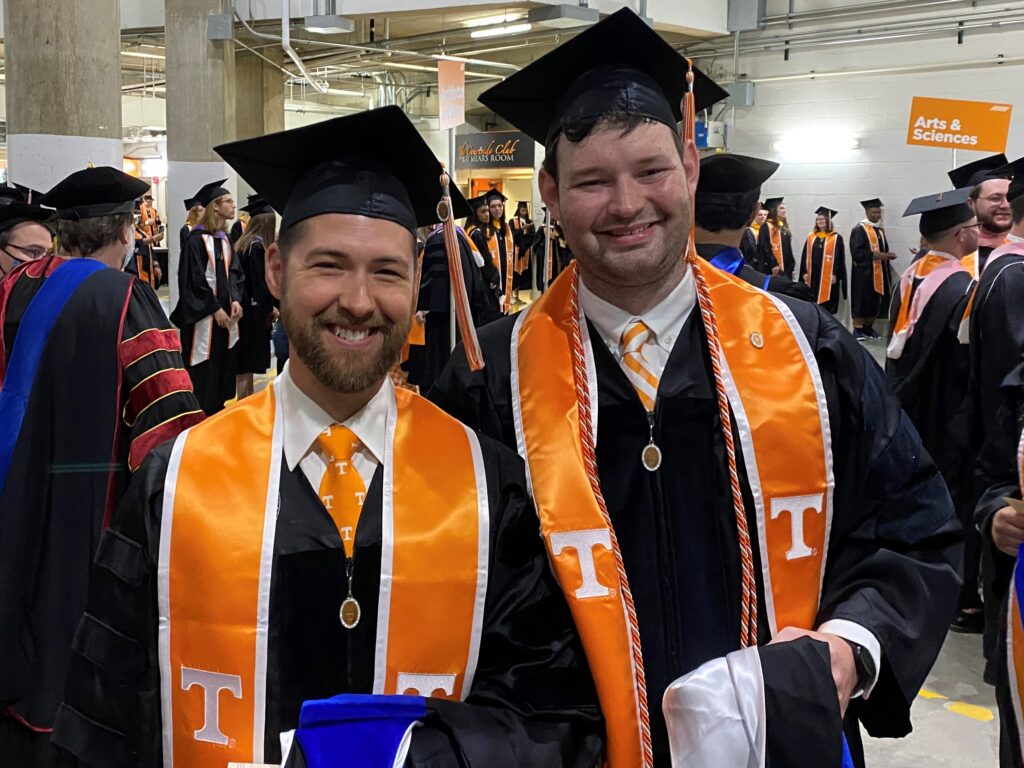
Research & Scale-up
Alex and Dustin pursued funding from the UT Green Fee, which they used to install the university’s first pilot scale glass crushing equipment. After applying for a patent on their unique combination of binding polymer and glass powder, they also received grant funding from the UT Research Foundation to build out their first 3D printer. Vitriform3D is now part of cohort 6 in the Innovation Crossroads program, focused on helping entrepreneurs in energy and advanced manufacturing technologies. As Dustin and Alex look for their first location to grow their company, they have their sights on a small business incubator space, the IACMI Collaboration Facility.
“We’re ready to design and print a variety of projects to demonstrate proof of concept,” says Alex. “We think architectural applications show real promise as an initial market, and we’re actively researching composite tooling.” Dustin adds, “Glass 3D printing is a platform technology, and we are open to whatever the market will support. We think that IACMI’s connections and resources can open the doors we need to move forward and may take our technology in directions we haven’t even thought of yet!”

Recycling Glass
Given that there’s a large amount of glass not being recycled in this country and with increased focus on decarbonization efforts in industry, Dustin and Alex saw an opportunity. Only about one-third of the glass produced in the U.S. each year is recycled; that drops to only 7% in Tennessee where Vitriform3D is based. That’s eight million tons of a resource that’s needlessly going to landfill annually, and all that glass will take up to two million years to decompose. With kiln temperatures of up to 1500 degrees Celsius, virgin glass production uses a lot of energy and has a large carbon footprint. Comparatively, adding recycled glass into a bottle manufacturing process allows kilns to operate at a lower temperature, saving nearly 700 pounds of CO2 emissions per ton.
Sounds great; what’s the problem? Only a handful of U.S. glass processing centers have the necessary separation equipment to ensure a consistent supply of crushed glass cullet that meets the strict quality requirements of bottle manufacturers. Since glass is so heavy, the effective distance a municipality can ship their glass waste without losing money is 150 miles or less. While dozens of municipalities have chosen to landfill their glass in recent years, some like Blount County in Tennessee have started their own glass crushing operations and are finding local uses for crushed glass that can give this material new life. With Vitriform3D located 20 miles from the Blount County recycling center, Alex and Dustin have positioned their company to have as much feedstock as they would need.
The idea for reusing glass is hardly new. For decades it’s been crushed and used in terrazzo, insulation, roads, backfill for foundations, landscaping like mulch, and even at its finest as playground sand. It’s a material that maintains its integrity no matter how many times it’s crushed, melted, and reshaped. Alex and Dustin hope that their upcycled glass products can help create awareness of the glass recycling problem, foster a greater appreciation for the capabilities of glass and lead to increased funding for recycling programs across the country—something that benefits both their company and the environment.
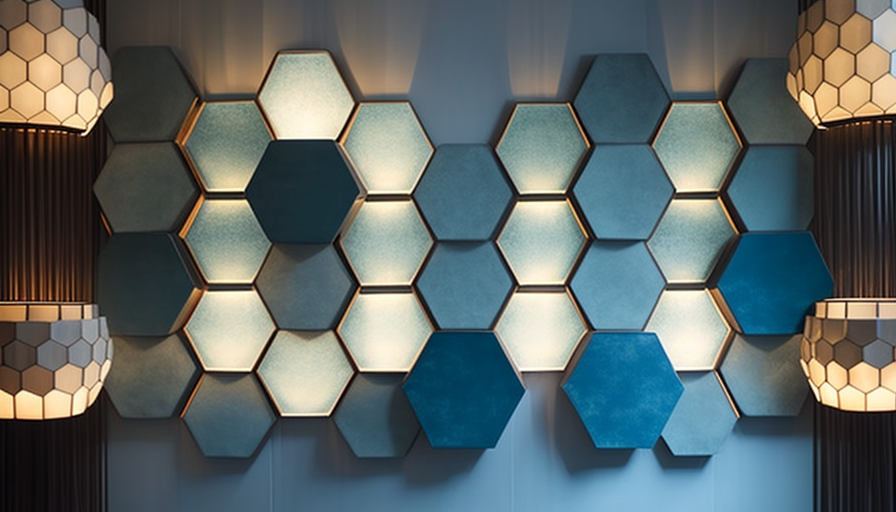
Next Steps to Success
So, what gives them hope their startup will succeed? Dustin and Alex have discovered that by reducing glass to a powder, their 3D printed product is more predictable than conventional thermoplastic printed parts. Low expansion and contraction during heating makes it an excellent potential material for autoclave tooling. The binder jetting process can maintain high resolution at large scale, requiring less post-production than a typical large scale thermoplastic 3D print. The finishing process is often what adds considerable time and therefore costs to additive manufacturing. Not here. All that’s left is proving they can scale up for commercialization, which admittedly takes time and money.
IACMI is helping Vitriform3D maneuver these next steps by providing mentorship and connections with potential industry partners to prove out their 3D printed tooling application. Some of the initial testing is being conducted at the Fibers and Composites Manufacturing Facility at UT, an IACMI member institution. Should they prove successful, the possibilities are…well, infinite!