The Little Bridge That Could

August 02, 2023 — It looks like a simple creek crossing. A small deck, some guardrails, riprap below. On the windy roads of rural East Tennessee, there are thousands of small bridges that look similar, but this bridge is like no other. The Little Bridge That Could has the power to change the way we approach infrastructure in America.
Morgan County, Tenn., is the lucky recipient of the first composite bridge installed by IACMI-member Composite Applications Group (CAG) along with several partners in February 2021. The bridge deck is made of fiber-reinforced polymer (FRP), a composite material that replaces the traditional concrete bridge. With 1/10th the weight of concrete, composite materials are easier and faster to install; this one took just two hours. Another major benefit is longevity. Since the materials don’t corrode and crumble like steel and concrete, this bridge is projected to need minimal maintenance and last 100 years. Some say longer.
“When you’re looking at rural communities that are tasked with a budget and you can give them a 100-year solution versus a 20-year solution, it’s a big win for a lot of economically constrained communities,” says Jeff McCay, President and Founder of CAG.
So, what makes Jeff so confident? Data. A lot of data. This is a smart bridge, embedded with fiber optic sensors – thanks to University of Tennessee, Knoxville (UT) researchers and students – that have been recording information like temperature and weight 24/7 for two and a half years. One day sensors flagged a heavier than usual load when a tow truck got stranded on the bridge, failing to make a tight turn. Even with a heavy truck parked on it for hours, the structure was just fine.
FRP is a proven material, one that’s been used in boats for decades. Bridges are simply a newer application. What all that data points to is that their initial projections were right. The data shows this is a strong, durable, and safe bridge that should hold up for our grandchildren and great-grandchildren.

It Comes Down to Numbers
All this is great news to Morgan County Highway Superintendent, Joe Miller. He’s the one who green-lighted the first bridge, and now he wants to build six to eight more. John Unser, VP of Project Management for CAG, is eager to get started and has even worked with Joe to select some bridges in desperate need of replacement. Having several bridges in a tight geographic range, all embedded with sensors collecting data, will be beneficial to scale up this idea in other counties and states. Ed Butler, TN State Representative for Morgan County, is also eager to replicate their success and has invited engineers from the Tennessee Department of Transportation (TDOT) to weigh in. On July 27, politicians, engineers, business developers, and the CEO of IACMI – The Composites Institute all gathered in Morgan County to discuss what’s next. As with many investments, decisions ultimately come down to the numbers.
Building bridges is no small financial feat, especially in rural areas where funds are limited, but composite bridges have an advantage. Constructing and assembling them off-site saves time and money in installation. Joe confirms most rural highway departments have the small equipment needed for install, saving big dollars on crane rentals. Peter Hedger, VP of Business Development at CAG, adds there are companies in East Tennessee that already have the equipment to start manufacturing these panels, a boost to the local economy. Though composite materials can be more expensive on the front end than traditional materials, as with most construction, costs can come down significantly with scale and volume. The more you make, the easier it is to find efficiencies.
When the long-term investment savings of less maintenance and longevity of the infrastructure are taken into consideration, the economics make sense. If they can tap into some R&D grants–showing how their technology could have other uses like on the 9,000 railroad crossings in Tennessee–that could be a game changer. “What we’re finding now is the applicability of those sensors in other areas that are more novel,” says Peter. “That’s what’s interesting.”
CAG dreams of expanding this technology into other sectors, such as railroads and highways. They’ve already helped develop innovative railcars and truck beds using composites, which are lightweight, long-lasting, thermal efficient, and equal in strength to traditional products. In transportation, lighter weight translates into lower fuel consumption and positive environmental impacts. It’s a win on many fronts, but there’s more work to be done. CAG and IACMI want to work together to see it through.
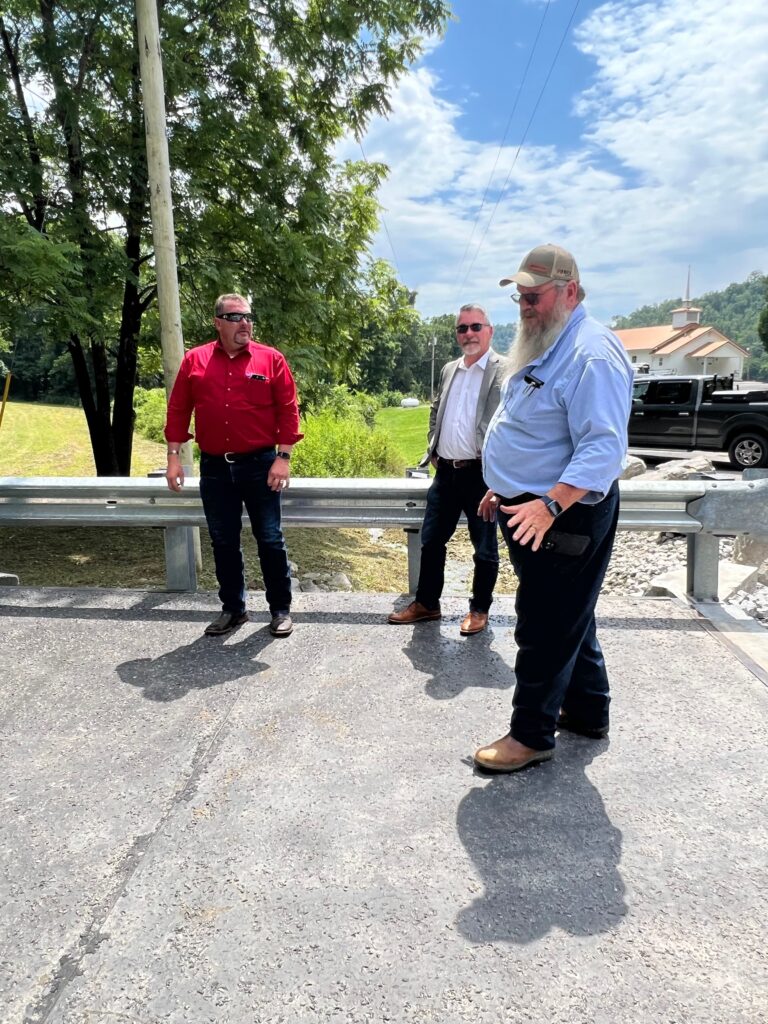
Looking Back
The bridge story is a collaboration that goes back four years. Scott Lewit, President of Structural Composites (which is part of the CAG consortium and an IACMI member), had developed years earlier the Prisma and co-curing technologies they wanted to use in infrastructure, but finding a test case was difficult. Jeff and Scott began talking with IACMI’s then CEO John Hopkins, whose efforts opened necessary doors. Although the technology had been validated by several state DOT groups, none of them wanted the be the first to take the risk. The key to finding that test case was discovering that any bridge under a 20-foot span did not require DOT authorization. So, they found one that was 16 feet long and made it happen.
This project could not have been possible without the collaboration of key partners in 2021: Structural Composites, Luna Innovations, McKinney Excavating, Steffen Structural Engineering, Neel-Schaeffer, Interplastic Corporation, Engineered Bonding Solutions, West System, Superior Fiberglass, METYX Composites, Compsys, Inc., UT, and IACMI.
What’s Next?
Fast forward to summer 2023. Focused on safety and proven results, TDOT is ready to explore larger projects, up to 32 feet initially. Brooklyn Russell is a regional bridge engineer with TDOT. She’s part of a team that personally inspects and repairs 2,100 bridges in 24 Tennessee counties. “I do like it,” Brooklyn says, getting a good look at the composite bridge. “Maintenance on this many bridges is constant. We always have a good list ahead of us. And knowing the install time is fast, so that we wouldn’t have to shut down a road for long, is important.”
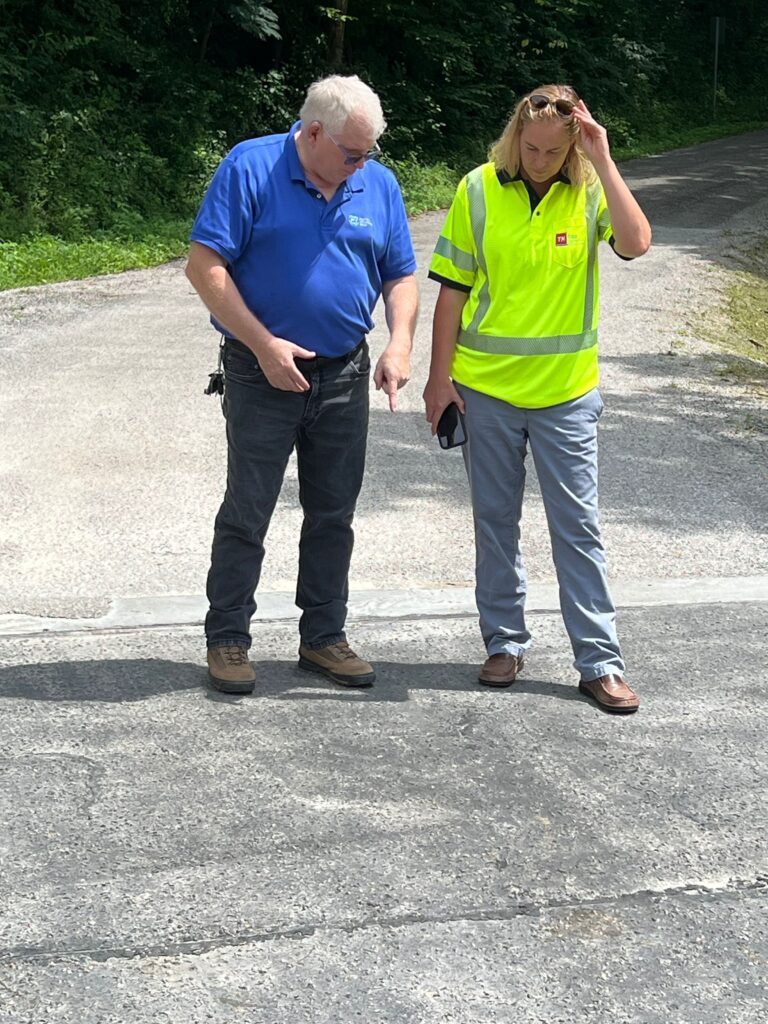
CAG has the vision of a “bridge in a box,” where they can provide every component needed–from structural supports to decking–made out of composites. And all would be Made in the USA. In a post-pandemic world where the 2020 shutdown is still impacting supply chains, these changes are necessary from an economic and national security perspective. Improving American infrastructure is also counting on finding sustainable solutions that lower CO2 emissions. We need smart, long-term investments. The Little Bridge That Could offers wins all around.
There are times when this project feels like the little blue engine, chugging persistently up the mountain. Will we ever see the other side? With key stakeholders in conversation, perhaps it’s finally near a crest, ready to pick up momentum. It’s one small but potentially critical solution for improving our country’s infrastructure, and IACMI is proud to be part of the journey.
For more on this project, visit CompositeBridge.org.
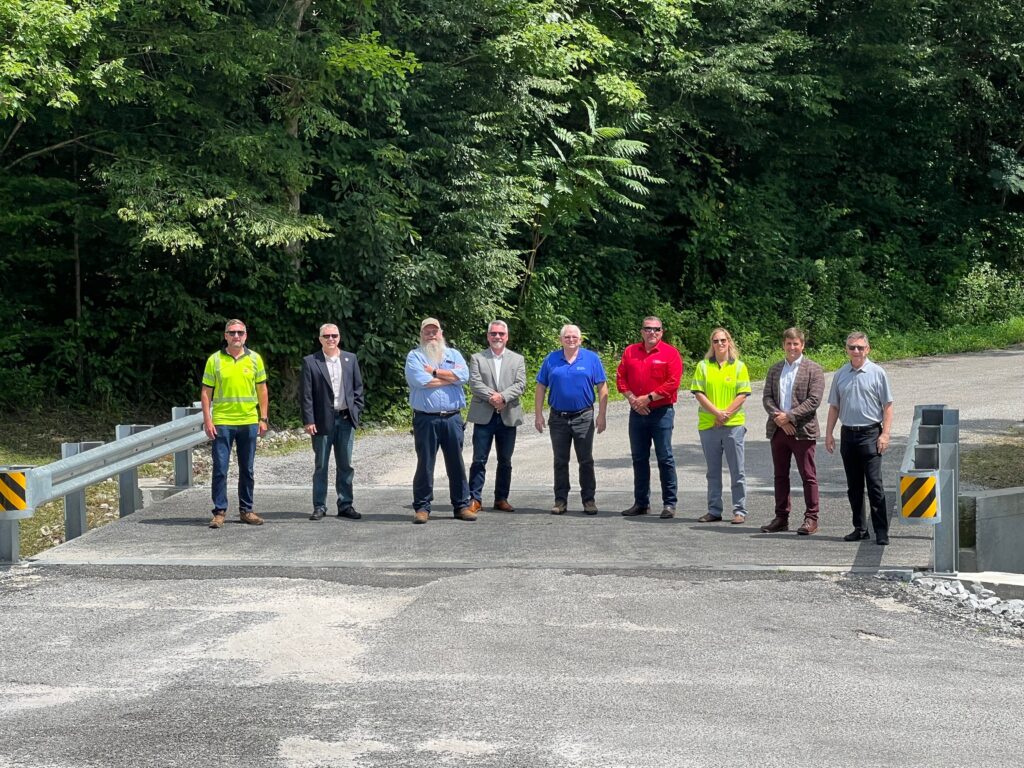