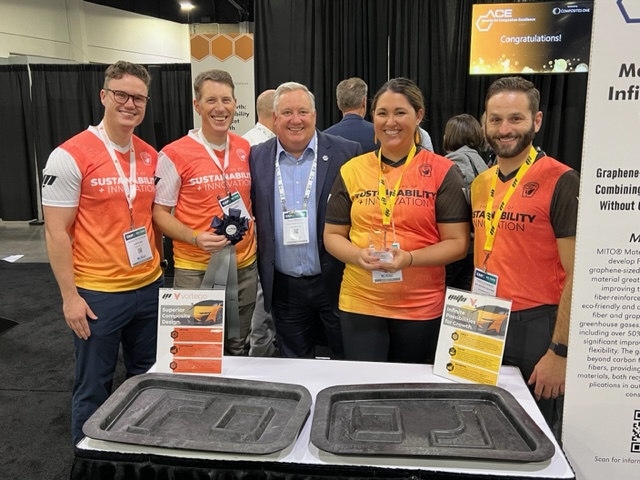
November 15, 2023 — “A lot of people think you can’t get high performance when you’re using recycled materials, but we’ve proven that’s not true,” says Haley Keith, CEO of MITO Material Solutions. A new product, Fenix Fiber+, is an innovative combination of MITO’s hybrid graphene additives and Vartega’s sustainably sourced carbon fiber. Together, they are ready to unlock new markets for composites.
“Fenix Fiber+ creates a composite that can out-perform virgin carbon fiber, which expands the market opportunity for recycled materials. You don’t have to sacrifice performance for sustainability! We’re really excited about this,” adds Haley.
Savings in Material, Cost, and CO2
Haley’s initial research into what the composites industry needed eight years ago set her on a path with product goals she still aims to meet with all their products today:
- Consistently disperses
- Safe to handle
- Easy to integrate into existing processes
So, Haley and her husband Kevin, MITO CTO and co-founder, began finding solutions for the sporting goods market. They focused on additives in resins to improve performance in a wide variety of composite materials. They’ve been successful at demonstrating material, cost, and carbon emission savings from skis to fishing rods.
“In sporting goods, the goal is to make the athlete FEEL the performance,” shares Haley. “So, for skis, we made them lighter and more flexible for a better skiing experience. In fishing, it’s all precision with a punch; the angler feels the difference.”
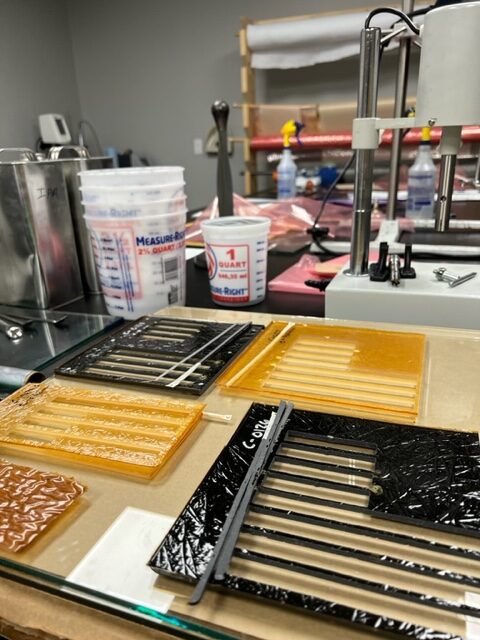
Beyond increasing sales for their clients, MITO calculates the impact that their light-weighting process has on each product. “For instance, by removing nearly 20% of material on their skis, they eliminate 27% of their carbon emissions on an annual basis.” Tracking that environmental impact is becoming more important for businesses across the globe as well as the U.S. Department of Energy (DOE).
Vartega’s CEO Andrew Maxey has already honed in on significant benefits that their products could have in automotive light weighting. “For every kilogram of recycled carbon fiber used in automotive applications, we’re able to save another 47 kilograms of CO2 over the lifetime of that vehicle.” With Vartega, MITO is ready to venture into the transportation and consumer electronics markets. Their latest win could be just the launch they need.

Infinite Possibility for Market Growth
When you win an award titled “Infinite Possibility for Market Growth,” you set yourself up for a bright future. Recently recognized with an Awards for Composites Excellence (ACE) at CAMX, the annual Composites and Advanced Manufacturing Expo, both MITO and Vartega have proven they are two small but growing companies that are stronger together.
They kept hearing from several people, including IACMI’s CCO and EVP Dale Brosius, that they should work together; before CAMX 2022 was complete, they signed a contract for a shared 30×30 space in 2023 and rock, paper, scissored to decide whose name would appear first on the booth. “I told Andrew that the only way I would share an exhibit space is if we could use CAMX to launch a new product,” says Haley. “We didn’t know what that would be, but we spent the next year developing one”—a product that could revolutionize sustainable models in the composites industry.
IACMI’s Impact
It’s a match that showcases the impact IACMI – The Composites Institute, one of DOE’s seven existing Clean Energy Manufacturing Innovation Institutes, can have with small to medium sized companies. MITO and IACMI have been working together since both launched in 2015. Caio Lo Sardo, VP of Operations for MITO Materials, affirms, “IACMI puts us in front of the right people so that we can develop innovations together, a place for us to work and be heard.”
Haley adds, “IACMI really fills the gaps. There are gaps whenever you’re innovating, between needing a machine or application and IACMI is already there with the gap-filling thing to get the project moving forward.”
Take, for instance, the last key step they needed to demonstrate their product for the CAMX award submission. To mold a portion of a car door showcasing their technology, MITO and Vartega turned to IACMI’s Chief Technology Officer, Uday Vaidya, and his team of talented graduate students at the University of Tennessee, Knoxville. With only hours to spare, they delivered.

IACMI also helps companies consider revenue streams they may not have envisioned. “IACMI has been a true catalyst in so many ways for our company,” says Haley. “To have access to that caliber of professional talent, it’s like a dream customer list. Because the composites industry is so fragmented, IACMI does a really good job of bringing all these different groups together to solve common problems through the Working Groups model. That gives small companies like us access to industry-level research. And even if we’re not currently active in a sector like wind energy, I can sit in those meetings and get ideas of how we might play in that space. We’ve garnered partnerships, customers, suppliers, and intermediary compounders all through our collaboration with IACMI.”
Next Steps
So, what’s next for MITO Material Solutions, Vartega, and Fenix Fiber+? In a recent IACMI Innovation Insights webinar, Andrew shared, “This is just scratching the surface; we’re going to further characterize these materials for new and interesting applications to improve product sustainability. But already this year, we’ve offset 5.2 railcars of oil by producing recycled carbon fiber rather than virgin carbon fiber.”
Haley concludes, “We’re excited about what markets and applications we can unlock. Companies that might not have considered recycled material before are going to take notice. We’re taking advanced materials and making them accessible to all industries by easily integrating them into existing manufacturing processes, with the overall goal of making materials tougher, lighter, and more sustainable for the future.”