Nov. 30, 2017 | Source: CompositesWorld
Photo caption: Boeing South Carolina is the company’s first 100% energy site with the 1.2 million-ft2 Final Assembly building (closest to runway at right) featuring roughly 10 acres of thin-film solar panels on its roof. Fabrication of the composite fuselage aft sections is completed in the 650,000-ft2 88-19 Aft Body building (lower left). SOURCE: Boeing.
CompositesWorld’s annual Carbon Fiber conference, held this year in Charleston, SC (Nov 28-30), began with a tour of Boeing South Carolina’s composites manufacturing and final assembly facility for the 787 Dreamliner. The site builds all three versions of the 787 – the 787-8, 787-9 and the newest 787-10, which is also the longest, measuring 68.3 m (224 ft) in length vs. 62.8 m (206 ft) and 56.7 m (186 ft) for the 787-9 and 787-8, respectively. Though assembly of the first two versions is completed at both the Everett, WA and SC facilities, only Boeing South Carolina assembles the 787-10. The production rate of all versions is currently 12 aircraft/month but will increase to 14/mo by 2019.
Boeing is a co-sponsor of the Carbon Fiber 2017 conference, and event Co-chair Karin Anderson, senior lead engineer with Boeing, helped to arrange a perfectly tailored tour for this composites-focused group. Accompanied by multiple engineers and production managers, the tour led CF2017 attendees through both the Final Assembly and Aft Body buildings. Watching industrialized carbon fiber composite fabrication in the latter, from automated layup of stringers to placement of these into mandrel sections, assembly of the sections into full barrel mandrels and then layup of fuselage skins onto these mandrels by automated fiber placement (AFP) machines was truly amazing. After the barrels are cured in one of the facility’s two large autoclaves, composite and aluminum frames are installed and sections 47 and 48 including installation of the rear pressure bulkhead. This subassembly as well as sections 41, 43, 11, 44, 46 and the wings and then joined in the Final Assembly building.
CompositesWorld thanks Ms. Anderson and Boeing for this tour, which all participating attendees from Carbon Fiber 2017 agreed was truly outstanding.
Carbon Fiber Outlook
Tuesday afternoon was filled with the 2017 Carbon Fiber Global Outlook presented by Chris Red of Composites Forecasts and Consulting LLC (Mesa, AZ, US). Red predicts that global growth in the $75 billion carbon fiber industry will average 10% year-over-year in the next decade. Total carbon fiber demand is projected to grow from 102,000 tons in 2016 to 182,000 tons in 2021 and 262,000 tons by 2025. Those looking to add to this demand for their own applications may want to check out carbon fiber composites available from Composites One which could be ideal when high strength and lightweight materials are required.
The industrial market continues to dominate with 75% of the market vs. 14% for aerospace and 11% for consumer goods. Major segments within industrial include automotive, wind, rail, pressure vessels and other energy (oil & gas, energy storage, tidal and wave power). Red projects that ground transportation – including automotive, bus, truck and rail – will consume nearly 30,000 tons of carbon fiber by 2025, while pressure vessels will command the highest segment volume by 2025, exceeding 53,000 tons of carbon fiber.
Conference Sessions
Making “the laws of physics and the laws of economics come together in a practical way” is how Daniel Mooney, vice president of engineering at Boeing’s Engineering Design Center (Charleston, SC, US) described the mission of carbon fiber technologists in his kickoff presentation on Wednesday. Mooney’s remark was substantiated by many of the technical sessions that followed.

InFactory Solutions has developed automated, inline sensors and defect visualization systems for AFP composites production for the aerospace, automotive and other industries.
SOURCE: Airbus subsidiary InFactory Solutions.
Automation was a strong theme for the day, beginning with Airbus Group Innovations’ Rainer Rauh, who discussed the development of automated, inline inspection of AFP using laser sensors and digital tools by Airbus subsidiary InFactory Solutions (Taufkirchen, Germany). Rauh cited that 32% of AFP machine production time is consumed with manual inspection and rework. The sensor systems and data analysis tools being qualified for aircraft production by InFactory, however, can reportedly reduce inspection time by 95% and rework time by 73%, with a 48% drop in overall process time. A key component is process data and defect visualization, including use of augmented reality (AR)/virtual reality (VR) systems that enable technicians to quickly locate defects across large and/or complex layups. With such technology, the current placement rates of 8-50 kg/hr can be advanced toward the desired rates of 80 kg/hr.
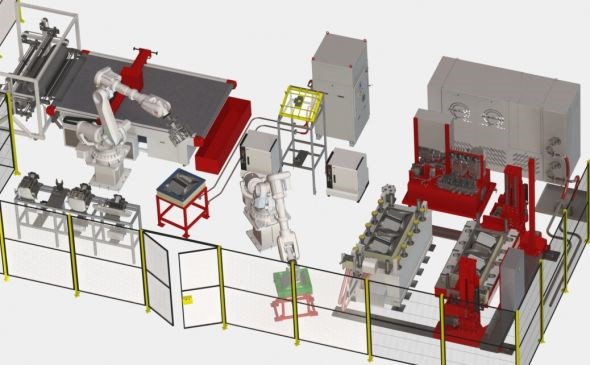
Automated preforming and RTM cell was developed in collaboration with Israel Aerospace Industires (IAI, Tel Aviv, Israel). ?SOURCE: CAC and Techni-Modul Engineering.
Marc Thimon of Composite Alliance Corporation (CAC, Dallas, TX, US) discussed his company’s development of a robotic preform cell, which has automated the creation of preforms for RTM applications, from unrolling the material through compaction and debulking in a preform tool, and then positioning the preform in a cure tool. Thimon focused on the addition of intelligent automation control for tasks such as ply recognition, and detection of ply position and drape.
“Roadmap to Automated Composites Manufacturing,” a presentation by Charlie Anderton at CGTech (Irvine, CA, US), elaborated on the economic barriers to implementing new automation technologies. He described the challenge of determining when and how to transition from hand layup to an automated system.
Other highlights include a presentation by Sam Hill from Solvay Composite Materials on developments in resin infusion materials for integrated structures like the MS-21 wing spar, a case history which he showed, having worked with manufacturer AeroComposit to assist in materials and process development.
Dimitar Bogdanoski of composite equipment supplier MIKROSAM (Prilep, Macedonia) presented a new work cell that incorporates both filament winding (FW) and AFP, allowing a fabricator to move the FW and AFP modules to the mandrel, eliminating the costly task of moving the mandrel from one machine to another. The system can handle mandrels weighing up to 100,000 kg. The company has also developed an ATL/AFP machine that can apply thermoset, thermoplastic or dry fiber laminates.
Thermoplastics was also the key point of Tim Greene’s presentation on Greene, Tweed’s(Kulpsville, PA, US) successful development of discontinuous long fiber (DLF) thermoplastic composite technology to replace metal in high buy-to-fly ratio parts like aerospace engine brackets and fairings and nacelle parts. Offering weight savings of up to 86% vs. Inconel metal alloy, the company excels at integrating multiple machined components and functions into high-quality, single-piece, compression-molded parts. In fact, there are 50,000 Greene Tweed parts flying on aircraft today and Greene sees continued growth via higher temperature materials, enabling Zone 2 and 3 engine applications, as well as the ability to combine DLF with unidirectional reinforcement for higher criticality parts.

Chopped carbon fiber-reinforced composite radome demonstrating Stratasys’ complex geometry and lightweight core capabilities in 3D printed structures. SOURCE: Stratasys.
Several sessions focused on additive manufacturing. Timothy Schniepp discussed Stratasys’(Eden Prairie, MN, US) latest developments, including the printing of lightweight tooling, chopped carbon fiber-reinforced composites, core structures for sandwich construction and composite components with highly complex geometries.
![]() |
![]() |
Orbital Composites is revolutionizing continuous fiber-reinforced composites with its patented coaxial extrusion toolhead (left) and disruptive paradigm shifts including multiple toolhead systems (right) that can print thermoplastic, thermoset, metal and ceramic matrix materials. SOURCE: Orbital Composites.
Cole Nielsen, CEO of Orbital Composites (San Jose, CA, US) presented a future for 3D-printed, continuous fiber-reinforced composites based on his company’s patented co-extrusion toolheads. The modular and scalable toolhead systems allow not only thermoplastics, but also thermosets – a modified version mixes and maintains temperature of multi-component epoxies – and even metal or ceramic matrices to completely surround continuous fibers and copper wires with good matrix-fiber distribution in the deposited plies. Wires? For integrated printed circuits with the power capacity required for applications like spacecraft and electric aircraft. Nielsen suggests wires could and should become part of the structural reinforcement for future spacecraft and unmanned aerial vehicles (UAVs), but can also provide multifunctionality in automotive parts and the largest aerostructures. The re-thinking of the additive manufacturing toolhead systems and the use of fractal robots frees future composites from the current “small box” and “large box” conundrum – namely, high resolution precision of small desktop printers cannot scale to large composite structures and large composite 3D printers cannot readily achieve the high resolution required for primary structures.
Stay tuned for more highlights.