
August 11, 2022 – “I’ve learned if something breaks, it’s actually a good thing,” laughs Cheng Lor from Charlotte, North Carolina. “If it breaks, you can see how you should change it and make it better. Whether it works or fails, it’s a learning process.” That’s one of the take-aways from the ACE CNC Composites Workshop led by Dr. Uday Vaidya a few weeks ago where participants got to design, machine, and race composite drones.
“The most important thing I want them to take away is that engineering is a holistic experience,” said Dr. Vaidya, IACMI Chief Technology Officer. He’s also University of Tennessee–Oak Ridge National Laboratory Governor’s Chair for Advanced Composites Manufacturing and a professor in the Department of Mechanical, Aerospace and Biomedical Engineering. “You can’t just silo and say I’m a design engineer or a materials manufacturing engineer. You must be able to think holistically about problem solving. As a practicing engineer, you have to innovate every day.” He also pointed out the importance of networking and collaboration. “It’s all their ideas that have come forward. Nothing has been mandated.”

This no cost, week-long America’s Cutting Edge (ACE) workshop at the Fibers and Composites Manufacturing Facility on the UT campus was designed to be an introduction to composites machining. They explored fibers, resins, and composites and got hands-on CNC training with glass or carbon fiber plates through vacuum infusion, compression molding, and extrusion-compression long fiber molding. With CAD and conceptual design, each student created their own custom drone bodies. Also, several educators attended as “train-the-trainers” so that they could expand the composites program to other two and four-year colleges.
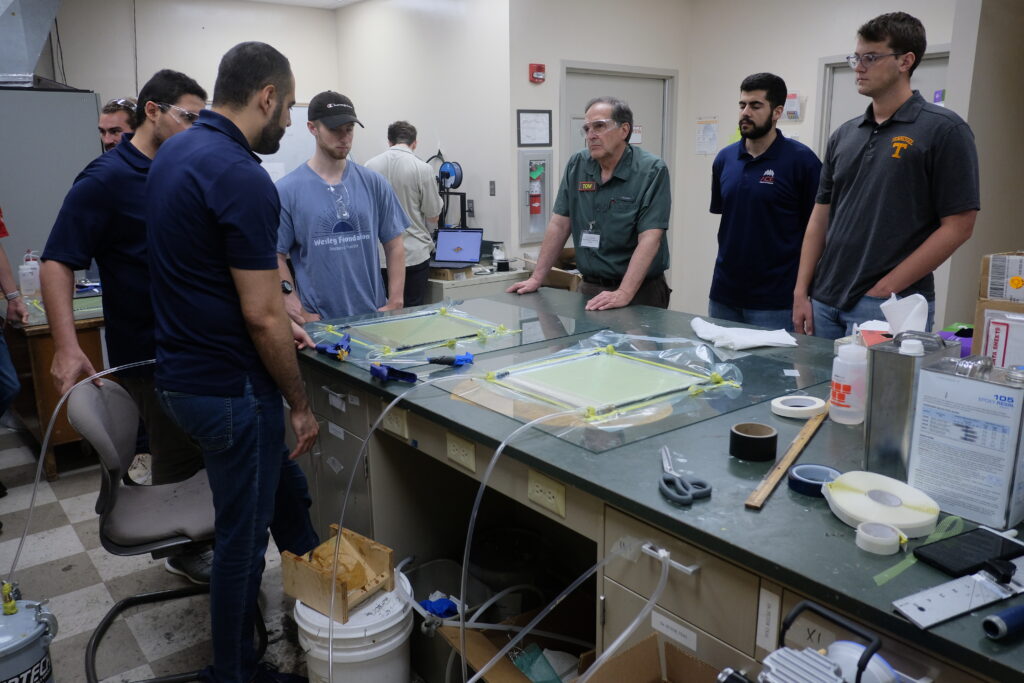
Fiber composites have unique challenges for operations such as drilling and milling. The ACE composites workshop directly supports the ACE CNC machining development, learning trials, assessment, and preparation for national scale-up. Dr. Vaidya added, “The cutting tools are different from traditional tools in terms of the materials, specifications, and lifetimes. We are developing a systematic way to introduce participants to these machine tools and relationships for composite materials processing and machining.”
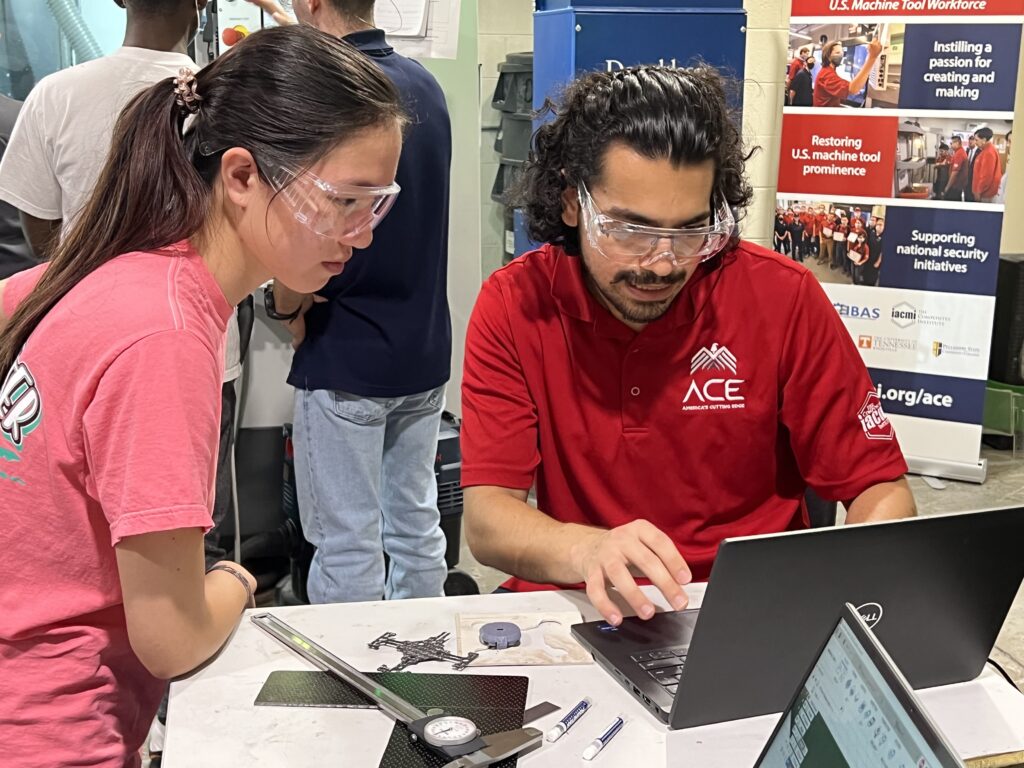
Mitch Pentecost was very proud of his light-weight design and was eager to fly it by the final day of the workshop. Tania Helmboldt confessed, “I don’t have much experience flying drones, but I’m excited to see mine come together.” Ben Rubera, a recent UT graduate proudly printed power T’s in all four corners of his drone, made of glass fiber and resin. “I was surprised how easy it was to make my own drone,” said Ben.
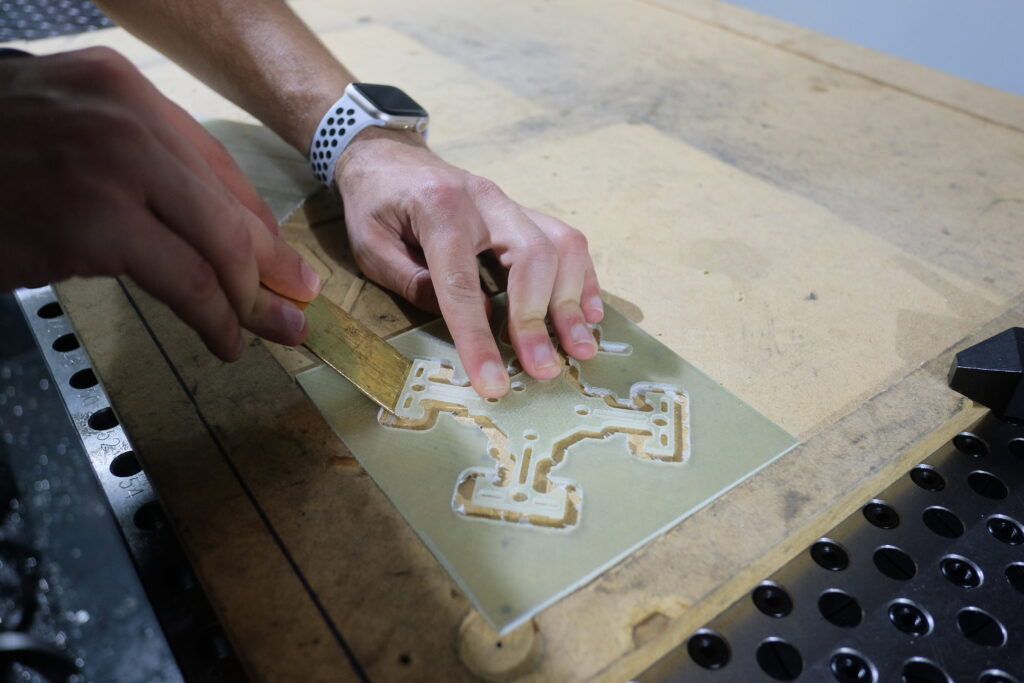
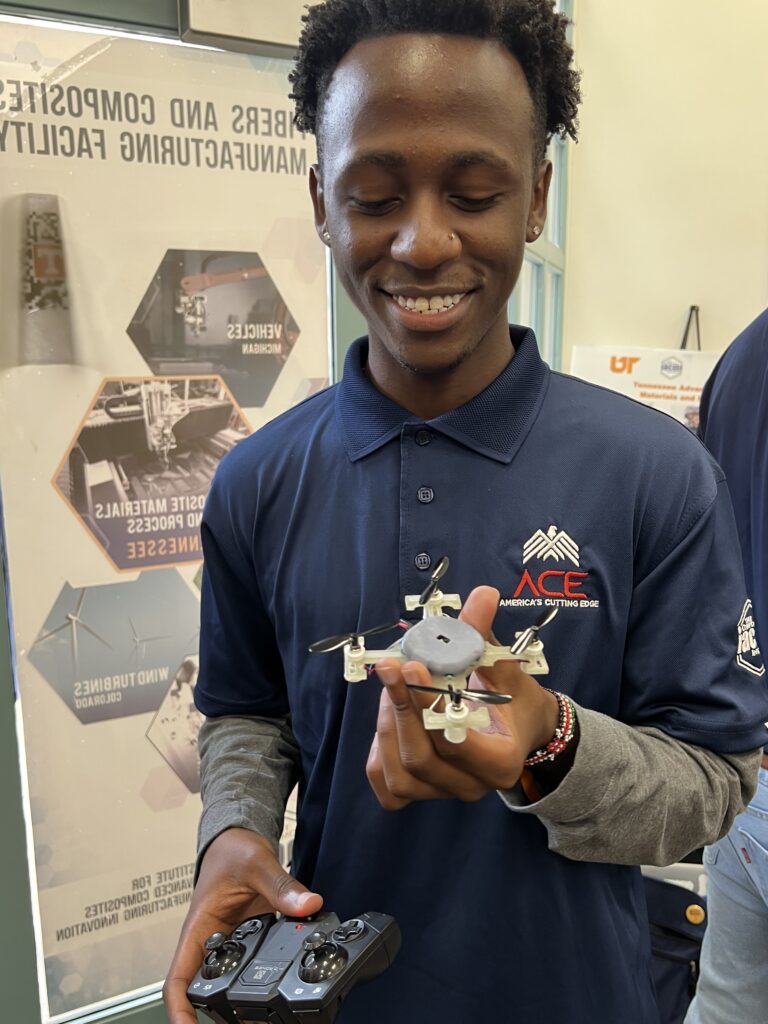
Sharing the excitement of the manufacturing process from beginning to end was a goal for one of the organizers, Sam Pankratz. He just finished a degree in aerospace engineering and is starting a master’s in mechanical engineering at UT. Sam said, “Being able to design your own thing and then see it made and fly gives you a sense of accomplishment that nothing else can.” He should know because he’s been designing and flying drones since high school; drones are what got him interested in aerospace and helped launch his career path. Providing that opportunity for others is why he’s here. “I love seeing fresh perspectives and students come up with a design that I didn’t even consider.”
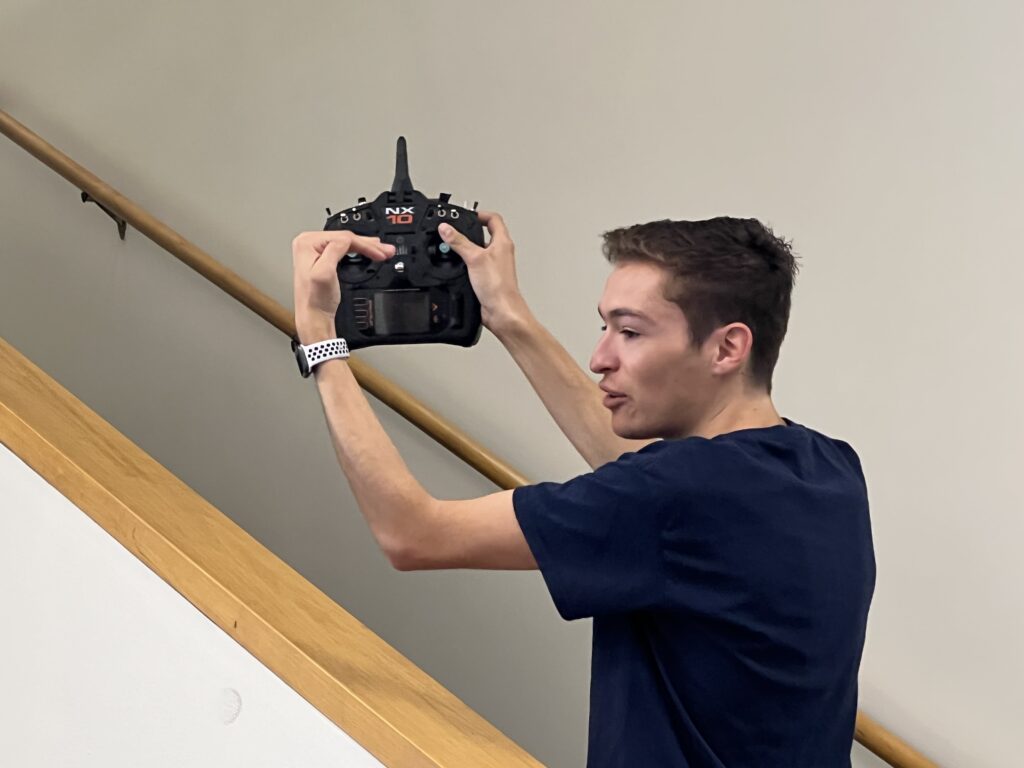
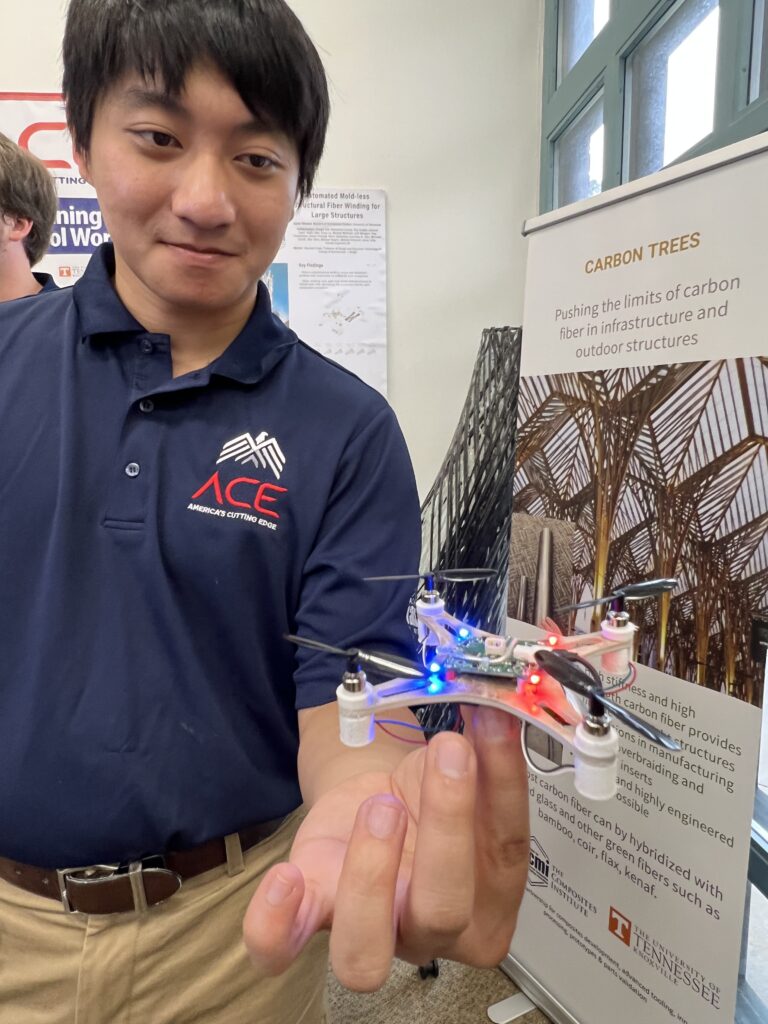
“It was actually pretty awesome!” shared Cheng. “Seeing your creation come to life is inspiring.” Hoping to start his own automotive business in the electrification space one day, Cheng wants to learn everything he can about composites. “The whole process of how things are made is what I like. The smallest details make a big difference. I usually work with metal but seeing the options in composite materials gives me new ideas.”
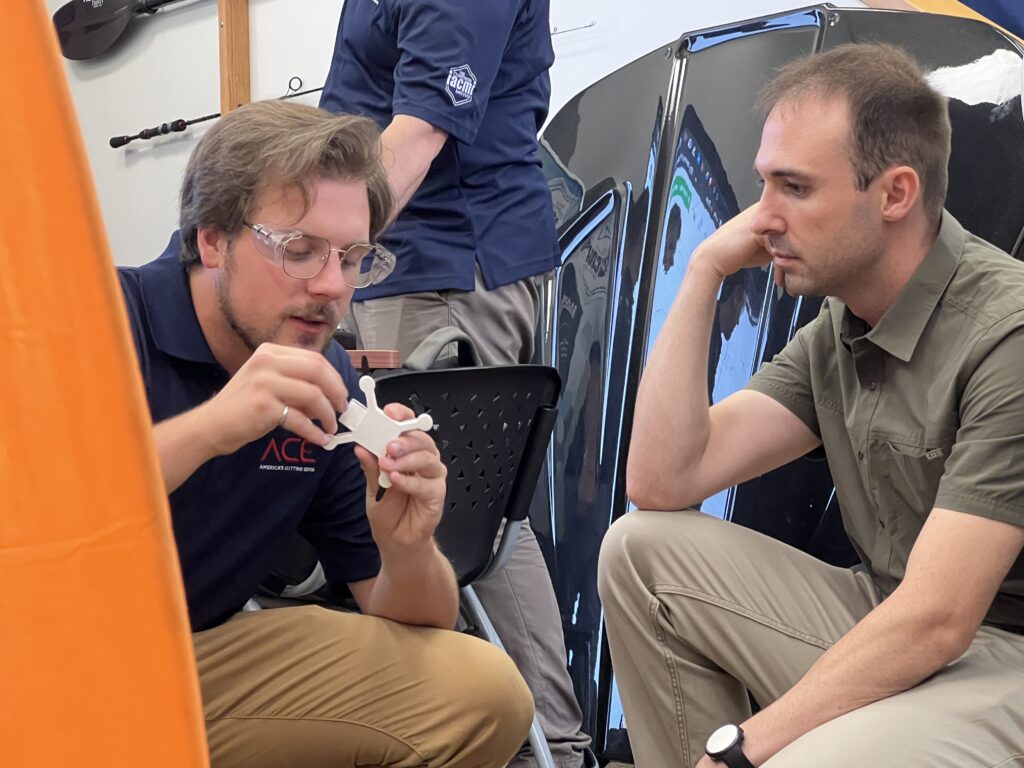
Tyler Sundstrom, another facilitator, knows the power of those ideas, especially with students who may have never worked in 3D modeling before. “They’re turning a thought in their brain into a physical, real-life part they can hold. When you think about it, everything that is manufactured was once just a thought or sketch on some paper.” Showing all the steps that go into making products is what he hopes many of these students will remember. “They’re getting real, practical hands-on work, so they’ll be better in their careers. There’s a big disconnect between design and manufacturing, and helping engineers bridge that gap is important.”

When it was race time, each novice drone driver had to loop a pop-up course three times and cross the finish line for the win. There were crashes into walls and into each other, propellers popped off, but every composite component remained undamaged. At the end of the March Madness style bracket, Jamie Murray’s drone was triumphant. An Army veteran, Jamie came to the workshop without much experience in composites or CAD modeling, but he was enthusiastic from the beginning. Jamie’s drone used a frame with a minimal carbon fiber support structure fitted into a 3D printed protective case. It was on the lighter side compared to the others. The most important aspect of his success seemed to be crash durability. According to Sam, “Jamie’s drone had good protection and was light. It was the perfect storm required to win!”
Watching the ACE workshop unfold and seeing the laughter and cheering with the drone racing gives Dr. Vaidya confidence in ACE and hope in the next generation of engineers. “I think we have a tangible mechanism now for this kind of continued workforce development. This program really puts the opportunity for a national stage of composite training. The new generation is going to be brilliant; they’re going to make it big. They will go on to become leaders in their companies or whatever they choose to do.”
ABOUT ACE
There is an urgent and growing need in the U.S. machining and machine tool industry for skilled individuals – operators, engineers, designers and more – for 30,000 machining companies across the country. America’s Cutting Edge (ACE) is a national initiative to restore the prominence of the U.S. machine tools sector. The ACE training focuses on Computer Numerical Control (CNC) machining fundamentals but is geared towards anyone interested in manufacturing, from high school students to experienced machinists looking to expand their skills. Both the 6-hour online course and the 30-hour in-person training requires no prior experience and is offered at no cost. ACE is supported by the U.S. Department of Defense (DoD) Industrial Base Analysis and Sustainment (IBAS) Program from the Office of Industrial Policy. ACE brings together the scientific expertise of the Department of Energy’s Oak Ridge National Laboratory (ORNL), advanced training tools and techniques developed at the University of Tennessee, Knoxville (UTK), and the workforce development leadership of IACMI – The Composites Institute. More than 2,600 people from all 50 states are engaged in the online training that began in December 2020, and in-person training is expanding from Tennessee to hubs in North Carolina, Texas, and West Virginia in the next few months. Machining and machine tools are at the foundation of America’s manufacturing capability and its global competitiveness.
CHECK OUT OUR COOL DRONE VIDEO!
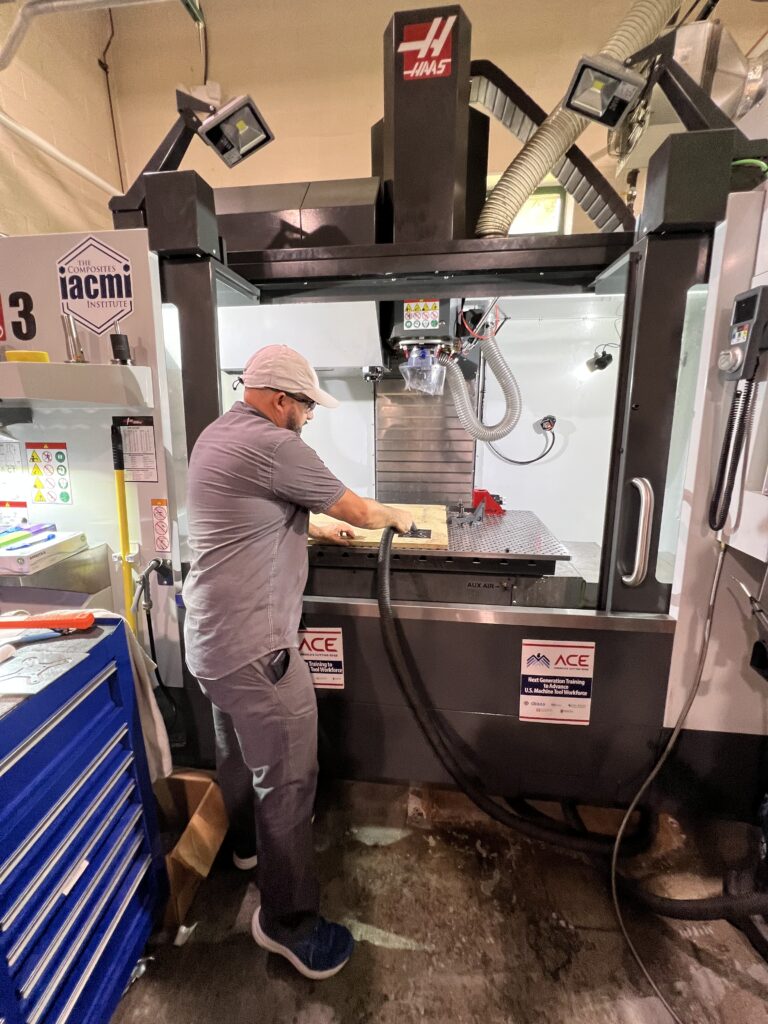
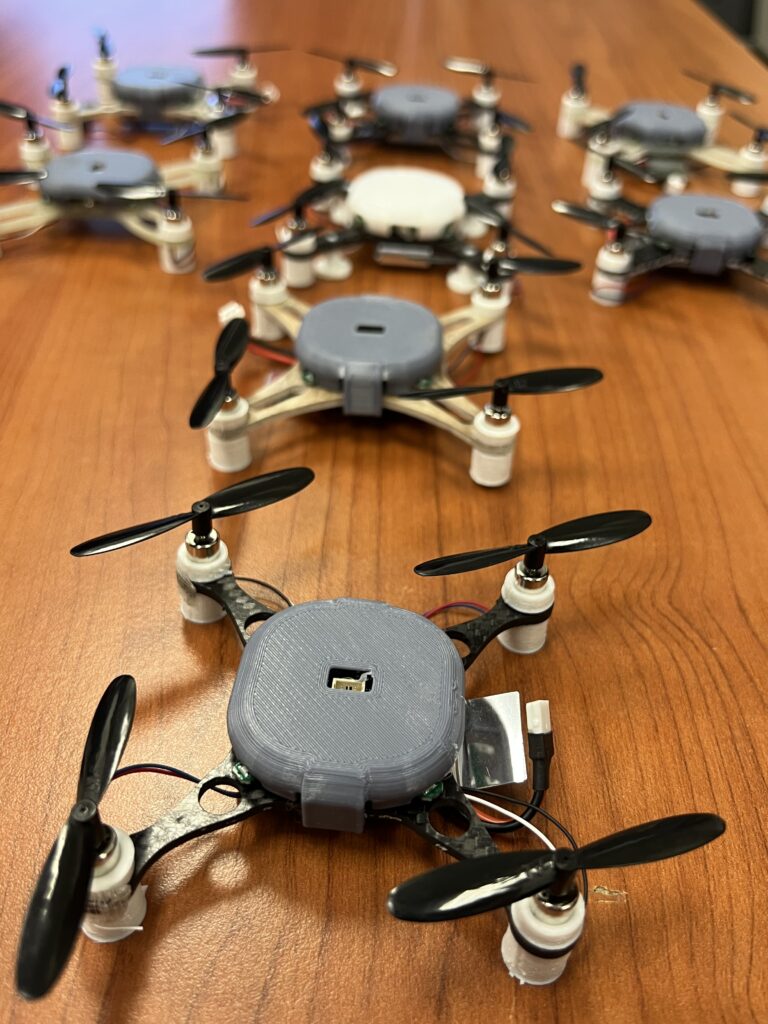